Budowa maszyn CNC na zamówienie to proces, który wymaga starannego planowania oraz uwzględnienia wielu kluczowych…
Budowa maszyn pneumatycznych
Budowa maszyn pneumatycznych opiera się na kilku kluczowych elementach, które współpracują ze sobą, aby zapewnić efektywne działanie całego systemu. Najważniejszym z nich jest sprężarka, która odpowiada za generowanie sprężonego powietrza. Sprężarka może być różnego rodzaju, w tym tłokowa, śrubowa czy wirnikowa, a jej wybór zależy od specyfiki zastosowania oraz wymaganej wydajności. Kolejnym istotnym elementem są zbiorniki ciśnieniowe, które przechowują sprężone powietrze i umożliwiają jego późniejsze wykorzystanie. Zbiorniki te muszą być odpowiednio zaprojektowane i wykonane z materiałów odpornych na wysokie ciśnienie. W systemach pneumatycznych niezbędne są także zawory, które kontrolują przepływ powietrza oraz jego kierunek. Zawory mogą być ręczne lub automatyczne, a ich odpowiedni dobór ma kluczowe znaczenie dla sprawności działania maszyny. Oprócz tego, do budowy maszyn pneumatycznych zalicza się również siłowniki pneumatyczne, które przekształcają energię sprężonego powietrza w ruch mechaniczny.
Jakie są zastosowania maszyn pneumatycznych w przemyśle
Maszyny pneumatyczne znajdują szerokie zastosowanie w różnych gałęziach przemysłu, co czyni je niezwykle wszechstronnymi narzędziami. W branży produkcyjnej wykorzystywane są do automatyzacji procesów montażowych oraz pakowania produktów. Dzięki swojej szybkości i precyzji maszyny pneumatyczne przyczyniają się do zwiększenia efektywności produkcji oraz redukcji kosztów pracy. W przemyśle motoryzacyjnym stosuje się je do obsługi linii montażowych, gdzie siłowniki pneumatyczne umożliwiają precyzyjne pozycjonowanie elementów oraz ich szybkie mocowanie. Również w branży spożywczej maszyny pneumatyczne odgrywają ważną rolę, szczególnie w procesach pakowania i transportu produktów. Dzięki zastosowaniu sprężonego powietrza możliwe jest bezpieczne i higieniczne przenoszenie żywności bez ryzyka jej uszkodzenia. W sektorze budowlanym maszyny pneumatyczne są wykorzystywane do obsługi narzędzi ręcznych, takich jak młoty udarowe czy wiertarki pneumatyczne, co znacznie ułatwia wykonywanie prac budowlanych.
Jakie są zalety i wady maszyn pneumatycznych
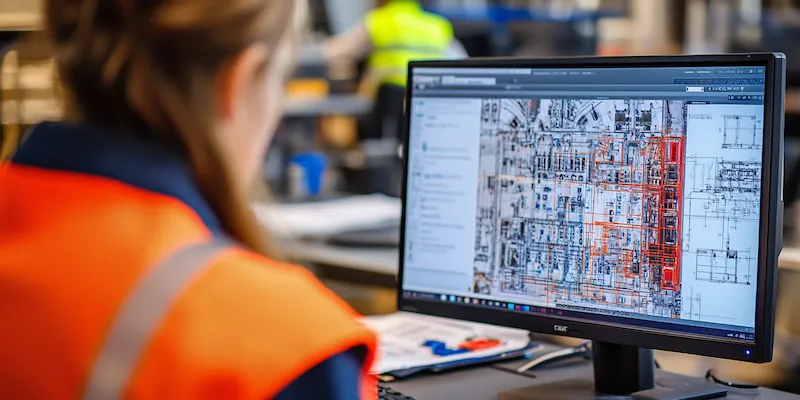
Budowa maszyn pneumatycznych
Maszyny pneumatyczne mają wiele zalet, które przyciągają uwagę inżynierów i przedsiębiorców. Jedną z głównych korzyści jest ich prostota konstrukcji oraz łatwość obsługi. Systemy pneumatyczne są zazwyczaj mniej skomplikowane niż hydrauliczne czy elektryczne, co przekłada się na mniejsze koszty serwisowania i konserwacji. Dodatkowo maszyny te charakteryzują się dużą niezawodnością oraz długą żywotnością, co sprawia, że inwestycja w nie jest często opłacalna na dłuższą metę. Kolejnym atutem jest możliwość pracy w trudnych warunkach środowiskowych, ponieważ sprężone powietrze nie stwarza zagrożenia wybuchowego ani nie zanieczyszcza otoczenia. Niemniej jednak maszyny pneumatyczne mają także swoje ograniczenia. Jednym z nich jest konieczność dostarczania sprężonego powietrza z zewnętrznego źródła, co może wiązać się z dodatkowymi kosztami związanymi z eksploatacją sprężarek i zbiorników ciśnieniowych. Ponadto wydajność systemów pneumatycznych może być ograniczona przez straty ciśnienia podczas transportu powietrza przez rury oraz przez nieszczelności w układzie.
Jakie innowacje technologiczne wpływają na rozwój maszyn pneumatycznych
W ostatnich latach obserwuje się dynamiczny rozwój technologii związanych z maszynami pneumatycznymi, co wpływa na ich efektywność oraz wszechstronność zastosowań. Innowacje te obejmują zarówno nowe materiały konstrukcyjne, jak i zaawansowane systemy sterowania. Przykładem mogą być nowoczesne siłowniki wykonane z lekkich kompozytów, które charakteryzują się większą odpornością na uszkodzenia mechaniczne oraz korozję. Dodatkowo rozwój technologii sensorów pozwala na dokładniejsze monitorowanie parametrów pracy systemów pneumatycznych, co zwiększa ich bezpieczeństwo oraz efektywność energetyczną. Nowoczesne systemy sterowania opierają się na automatyce przemysłowej i umożliwiają integrację maszyn pneumatycznych z innymi urządzeniami w zakładzie produkcyjnym. Dzięki temu możliwe jest osiągnięcie lepszej synchronizacji procesów oraz optymalizacja zużycia energii. Warto również zwrócić uwagę na rozwój technologii odzysku energii sprężonego powietrza, co pozwala na zmniejszenie kosztów eksploatacji systemów pneumatycznych poprzez ponowne wykorzystanie energii generowanej podczas pracy maszyn.
Jakie są najczęstsze problemy w budowie maszyn pneumatycznych
Budowa maszyn pneumatycznych, mimo swoich licznych zalet, wiąże się również z pewnymi wyzwaniami i problemami, które mogą wystąpić w trakcie eksploatacji. Jednym z najczęstszych problemów jest nieszczelność układu pneumatycznego, która może prowadzić do utraty ciśnienia i obniżenia efektywności działania maszyny. Nieszczelności mogą występować w różnych miejscach, takich jak połączenia rur, zawory czy uszczelki. Dlatego regularne przeglądy i konserwacja systemu są kluczowe dla zapewnienia jego prawidłowego funkcjonowania. Innym istotnym problemem jest zanieczyszczenie sprężonego powietrza, które może wpływać na jakość pracy maszyn oraz ich żywotność. Zanieczyszczenia mogą pochodzić z otoczenia lub z samej sprężarki, dlatego stosowanie filtrów powietrza oraz odpowiednich procedur czyszczenia jest niezbędne. W przypadku maszyn pneumatycznych należy również zwrócić uwagę na odpowiednie smarowanie elementów ruchomych, ponieważ brak smarowania może prowadzić do szybkiego zużycia komponentów. Dodatkowo, niewłaściwe dobranie parametrów pracy systemu, takich jak ciśnienie robocze czy przepływ powietrza, może skutkować nieefektywnym działaniem maszyny oraz zwiększonym zużyciem energii.
Jakie są różnice między maszynami pneumatycznymi a hydraulicznymi
Maszyny pneumatyczne i hydrauliczne to dwa różne typy systemów mechanicznych, które mają swoje unikalne cechy oraz zastosowania. Główna różnica między nimi polega na medium roboczym – w systemach pneumatycznych wykorzystywane jest sprężone powietrze, podczas gdy w hydraulicznych stosuje się cieczy, zazwyczaj oleje hydrauliczne. Ta różnica ma istotny wpływ na właściwości obu systemów. Maszyny pneumatyczne charakteryzują się mniejszą siłą generowaną przez siłowniki w porównaniu do systemów hydraulicznych, co sprawia, że są bardziej odpowiednie do aplikacji wymagających mniejszych obciążeń i szybkich ruchów. Z drugiej strony, maszyny hydrauliczne oferują znacznie większą moc i precyzję w kontrolowaniu ruchu, co czyni je idealnymi do ciężkich prac budowlanych czy przemysłowych. Kolejną różnicą jest sposób działania – systemy pneumatyczne są bardziej elastyczne i łatwiejsze do rozbudowy, a także mniej podatne na awarie związane z nieszczelnościami. Hydraulika natomiast wymaga bardziej skomplikowanej infrastruktury oraz regularnej konserwacji ze względu na ryzyko wycieków cieczy.
Jakie są kluczowe zasady bezpieczeństwa przy pracy z maszynami pneumatycznymi
Bezpieczeństwo pracy z maszynami pneumatycznymi jest niezwykle istotne zarówno dla operatorów tych urządzeń, jak i dla innych pracowników znajdujących się w ich pobliżu. Kluczową zasadą jest regularne szkolenie personelu dotyczące obsługi i konserwacji sprzętu pneumatycznego. Pracownicy powinni być świadomi potencjalnych zagrożeń związanych z używaniem sprężonego powietrza oraz umieć rozpoznać objawy awarii czy nieszczelności. Kolejnym ważnym aspektem jest stosowanie odpowiednich środków ochrony osobistej, takich jak gogle ochronne czy rękawice, które mogą chronić przed urazami mechanicznymi oraz działaniem sprężonego powietrza. Należy także przestrzegać zasad dotyczących ciśnienia roboczego – każdy system powinien być dostosowany do maksymalnego ciśnienia określonego przez producenta. Ważne jest również regularne przeprowadzanie inspekcji technicznych oraz konserwacji urządzeń, co pozwala na wczesne wykrycie potencjalnych usterek i uniknięcie poważnych awarii. Dodatkowo warto zadbać o odpowiednie oznakowanie strefy pracy maszyn pneumatycznych oraz zapewnienie dostępu do instrukcji obsługi w widocznych miejscach.
Jakie trendy kształtują przyszłość budowy maszyn pneumatycznych
Przyszłość budowy maszyn pneumatycznych kształtowana jest przez wiele trendów technologicznych oraz zmieniające się potrzeby rynku. Jednym z najważniejszych kierunków rozwoju jest automatyzacja procesów przemysłowych, która wymusza na producentach dostosowanie swoich rozwiązań do nowoczesnych standardów automatyki i robotyki. W tym kontekście rośnie znaczenie integracji maszyn pneumatycznych z systemami sterowania opartymi na sztucznej inteligencji oraz Internetu Rzeczy (IoT). Dzięki temu możliwe będzie zbieranie danych o wydajności maszyn oraz ich optymalizacja w czasie rzeczywistym. Kolejnym istotnym trendem jest dążenie do zwiększenia efektywności energetycznej systemów pneumatycznych poprzez rozwój technologii odzysku energii oraz zastosowanie nowoczesnych materiałów izolacyjnych. Wzrasta także zainteresowanie ekologicznymi rozwiązaniami, które mają na celu minimalizację wpływu produkcji i eksploatacji maszyn na środowisko naturalne. Warto również zauważyć rosnącą popularność modułowych rozwiązań konstrukcyjnych, które pozwalają na łatwe dostosowywanie układów pneumatycznych do zmieniających się potrzeb produkcyjnych bez konieczności przeprowadzania skomplikowanych modernizacji całego systemu.
Jakie są koszty budowy i eksploatacji maszyn pneumatycznych
Koszty budowy i eksploatacji maszyn pneumatycznych mogą się znacznie różnić w zależności od wielu czynników, takich jak rodzaj zastosowanej technologii, skomplikowanie konstrukcji oraz specyfika zastosowań przemysłowych. Na etapie budowy kluczowe znaczenie ma wybór odpowiednich komponentów – sprężarek, zbiorników ciśnieniowych czy zaworów – które będą odpowiadały wymaganiom danego procesu produkcyjnego. Koszt zakupu tych elementów może stanowić znaczną część całkowitych wydatków związanych z inwestycją w maszyny pneumatyczne. Dodatkowo należy uwzględnić koszty instalacji oraz uruchomienia systemu, które mogą być różne w zależności od stopnia skomplikowania układu oraz wymagań dotyczących infrastruktury zakładowej. Po uruchomieniu maszyny istotne są koszty eksploatacyjne związane z energią elektryczną potrzebną do napędu sprężarek oraz kosztami serwisowania i konserwacji urządzeń. Regularna konserwacja ma kluczowe znaczenie dla zapewnienia długotrwałego działania systemu oraz minimalizacji ryzyka awarii, co wiąże się z dodatkowymi wydatkami. Warto także pamiętać o kosztach związanych z ewentualnymi naprawami czy wymianą uszkodzonych elementów układu pneumatycznego.